Достоинствами пайки являются простота и дешевизна технологического процесса, широкие возможности его механизации и автоматизации, возможность соединения всех металлов и разнородных материалов (металл с керамикой, стеклом, резиной), малые остаточные температурные напряжения и деформации, малое электросопротивление мест соединения. Так как непосредственная пайка при соединении металлов с неметаллами невозможна, то на поверхности неметаллических материалов создают промежуточный слой из меди, никеля, серебра, который хорошо сцепляется с поверхностью этих материалов и обеспечивает качественную пайку с металлом.
Недостатком соединений пайкой является их невысокая механическая и термическая прочность.
Различают паяные соединения внахлестку и встык. Наибольшую прочность имеет соединение внахлестку, но при этом увеличиваются габариты соединения. Соединение встык имеет малые габариты, но невысокую прочность.
Заклепочные соединения
Заклепочные соединения выполняют с помощью специальных крепежных деталей – заклепок (рис. 3, а, б) или непосредственным расклепыванием цапф деталей (рис. 3, в, г).
Заклепка представляет собой цилиндрический стержень с двумя головками, одна из которых, называемая закладной, выполнена заранее, а вторая, замыкающая, получается в процессе сборки под ударами инструмента. Соединяемые детали при этом сильно сжимаются.
Рис. 3
Форма и размеры заклепок стандартизированы. Стержень заклепки может быть сплошным или полым; головки по форме бывают полукруглые (рис. 4, а), потайные (рис. 4, б), полупотайные (рис. 4, в), плоские (рис. 4, г). Заклепки изготавливают из пластичных материалов: низкоуглеродистых сталей (Ст2, Ст3, 08, 10), меди (М1), латуни (Л62), алюминиевых сплавов. Материал соединяемых деталей может быть тверже или мягче материала заклепок. Желательно, чтобы коэффициенты линейного расширения заклепок и соединяемых деталей были равными или близкими друг другу. В противном случае при изменении температуры возникнут дополнительные напряжения, что снизит прочность соединения. Диаметр d (см. рис. 4, а) заклепки принимают примерно в 1,8 … 2,0 раза больше минимальной толщины соединяемых деталей. Стержень заклепки должен выступать над соединяемыми деталями на величину примерно 1,5d для образования замыкающей головки. Для обеспечения лучшей механической прочности и предотвращения концентрации напряжений при посадке и клепке заклепки рекомендуют минимальный зазор между заклепкой и стенками отверстия. Диаметр отверстия под заклепку принимают на 0,2 … 0,5 мм больше диаметра заклепки.
Заклепочные соединения применяют для соединения трудносвариваемых металлов и разнородных материалов; в конструкциях, подверженных действию вибрационных и ударных нагрузок; для соединения металлических деталей с неметаллическими.
Выбор формы заклепки зависит от материала и толщины соединяемых деталей.
Стальные заклепки применяют для прочных соединений, а латунные и алюминиевые – для соединений, не требующих большой механической прочности. Для соединения деталей, изготовленных из хрупких или неметаллических материалов, используют полупустотелые и пустотелые заклепки (рис. 4, д, е).
Заклепки с полукруглой головкой – самые распространенные и применяются везде, где допустима выступающая головка. Применение заклепок с потайной головкой целесообразно для деталей из прочных материалов при толщине более 2 … 2,5 мм. При меньшей толщине берут заклепки с полупотайной головкой. Для соединения мягких и эластичных материалов (винипласт, резина) необходимы большие площади головки, поэтому под заклепки ставят шайбы, прокладки. Клепка и развальцовка заклепок не должны сильно деформировать соединяемые детали.
??????????? ?????????? ????????? ?????????? (???. 5, ?) ??? ????? ? ????? (???. 5, ?) ??? ????? (???. 5, ?) ?????????? ? ????????????? ???????? ? ????, ??? ??? ????? ???????????? (???. 5 ?) ??? ????????? ????.
Рис. 5
Шаги между заклепками выбираются исходя из назначения соединения и удобства клепки: t = (2 … 8)d, ℓ = (1,35 … 2)d, m = (1,5 … 2)d. Заклепки рассчитывают на сдвиг по поперечным сечениям и на смятие по боковым поверхностям, а листы – на растяжение по ослабленным отверстиями под заклепки сечениям.
Достоинствами заклепочных соединений являются возможность соединения различных материалов, хорошая сопротивляемость вибрационным и ударным нагрузкам, удобство и надежность контроля качества соединения. К недостаткам относятся трудоемкость (разметка, сверление отверстий, закладка и клепка заклепок) и высокая стоимость; ослабление соединяемых деталей отверстиями; дополнительный расход материала на накладки.
Клеевые соединения
Склеиванием называют соединение деталей тонким слоем быстротвердеющего раствора – клея. Процесс склеивания состоит из подготовки соединяемых поверхностей деталей, нанесения клея, соединения деталей и выдержки при определенных давлении и температуре.
Клеевые соединения применяют для скрепления деталей из различных металлических и неметаллических (стекло, керамика, пластмасса) материалов в любом их сочетании. К клеевым соединениям не предъявляют требований высокой прочности, но они должны хорошо сопротивляться вибрациям, воздействию влаги, колебаниям температур. Соединения бывают чисто клеевые и клеемеханические, для повышения герметичности (клеерезьбовые, клеесварные). Клеевые соединения улучшают герметизацию, снижают стоимость изделия и позволяют проще решать задачи миниатюризации конструкций. Их часто применяют в тех случаях, когда невозможно механическое крепление соединяемых деталей, например, склеивание оптического стекла с помощью прозрачных и неокрашенных клеев, крепление полупроводникового кристалла с кристаллодержателем.
Прочность клеевого соединения зависит от способа подготовки поверхностей. Желательно, чтобы они были шероховатые. Для этого применяют механическую (абразивную) и химическую (травление в растворах) обработку. Клеевой слой для повышения прочности должен быть по возможности тонок (0,05 … 0,25 мм), тепло- и влагостойким, не подвергаться старению. Для обеспечения необходимого взаиморасположения склеиваемых деталей в конструкции предусматривают фиксирующие элементы – выступы, впадины и т.п.
Клеи подбирают исходя из свойств материала соединяемых поверхностей. Клеи делят на твердеющие при удалении растворителя, твердеющие при охлаждении расплава и твердеющие за счет химических процессов.
Процесс склеивания клеями первой группы сводится к нанесению на поверхность деталей раствора клея, сдавливанию деталей и последующему удалению растворителя путем испарения или впитывания в склеиваемый материал. Соединение обладает свойством обратимости, его не применяют для изделий, работающих в условиях повышенной влажности и температуры. К таким клеям относят резиновые, казеиновые и другие виды клеев.
Клеи второй группы перед нанесением разжижают нагреванием, затем наносят на поверхности, которые сдавливают и выдерживают при комнатной температуре. Эти клеи также обратимы, т.е. при нагревании становятся вязкими, и соединения разрушаются.
Клеи третьей группы необратимы, полученное с их помощью соединение обладает большой прочностью, однако процесс склеивания бывает сложным, некоторые клеи твердеют при нагревании соединения. К таким клеям относят синтетические клеи серий БФ, «Момент», клеи на эпоксидной, эпоксидно-кремнийорганической основе и др.
Клеевое соединение лучше работает на сдвиг, хуже – на отрыв. Его прочность зависит от сорта клея, толщины и качества слоя, прочности сцепления клея с поверхностями соединяемых деталей.
Соединения заформовкой и запрессовкой
Заформовка заключается в соединении металлических элементов (арматуры) со стеклом, пластмассами, резиной, легкоплавкими цинковыми, алюминиевыми и магниевыми сплавами путем погружения этих элементов в формуемый материал, находящийся в вязкотекучем пластичном или жидком состоянии. После застывания формуемого материала образуется неразъемное соединение.
Таким способом получают различные рукоятки (рис. 6), крышки, клеммовые держатели, детали для электроизмерительных, оптико-механических и электронных приборов. Заформовка является единственным способом получения газонепроницаемого соединения металлических электродов со стеклянными баллонами электровакуумных устройств.
Соединения заформовкой имеют следующие достоинства: не требуются высокие точность и чистота обработки погружаемых частей арматуры; можно получить необходимые, часто не совместимые местные свойства элементов узла – электро- и теплопроводность арматуры при сохранении изоляционных свойств узла; уменьшаются масса изделий и расход металла, стоимость.
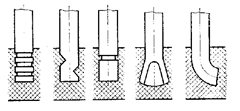
Рис. 6
При заформовке практически отсутствует сцепление арматуры с формуемым материалом. Прочность и плотность соединений обеспечивают выбором соответствующих форм погружаемой арматуры в виде кольцевых проточек, впадин, уступов, уширений, загибов (см. рис. 6), увеличивающих поверхности контакта и препятствующих ее выдергиванию.
Соединения запрессовкой получают путем создания гарантированного натяга между охватываемой и охватывающей поверхностями при сборке. После сборки вследствие упругих и пластических деформаций на поверхности контакта возникает удельное давление и соответствующие ему силы трения, препятствующие взаимному смещению деталей.