Реферат: Основные механические характеристики материалов
Следующей характеристикой является предел текучести --- напряжение, при котором происходит рост деформации без заметного увеличения нагрузки. В тех случаях, когда на диаграмме отсутствует явно выраженная площадка текучести, за предел текучести принимается условно величина напряжения, при котором остаточная деформация eост = 0,002 или 0,2% (рис. 6). В некоторых случаях устанавливается предел eост =0,5%.
Рис. 6
Условный предел текучести обозначается через s0.2 и s0.5 зависимости от принятой величины допуска .на остаточную деформацию. Индекс 0,2 обычно в обозначениях предела текучести опускается. Если необходимо отличить предел текучести на растяжение от предела текучести на сжатие, то в обозначение вводится соответственно дополнительный индекс «р» или «с». Таким образом, для предела текучести получаем обозначения sтр и sст .
Предел текучести легко поддается определению и является одной из основных механических характеристик материала.
Отношение максимальной силы, которую способен выдержать образец, к его начальной площади поперечного сечения носит название предела прочности, или временного сопротивления, и обозначается через sвр ( сжатие — sвс ).
sвр не есть напряжение, при котором разрушается образец. Если относить растягивающую силу не к начальной площади сечения образца, а к наименьшему сечению в данный момент, можно обнаружить, что среднее напряжение в наиболее узком сечении образца перед разрывом существенно больше, чем sвр . Таким образом, предел прочности также является условной величиной. В силу удобства и простоты ее определения она прочно вошла в расчетную практику как основная сравнительная характеристика прочностных свойств материала.
Рис. 7
При испытании на растяжение определяется еще одна характеристика материала — удлинение при разрыве d %.
Удлинение при разрыве представляет собой величину средней остаточной деформации, которая образуется к моменту разрыва на определенной стандартной длине образца. Определение d %. производится следующим образом.
Перед испытанием на поверхность образца наносится ряд рисок, делящих рабочую часть образца на равные части. После того как образец испытан и разорван, обе его части составляются по месту разрыва (рис. 7). Далее, по имеющимся на поверхности рискам от сечения разрыва вправо и влево откладываются отрезки, имевшие до испытания длину 5d (рис. 7). Таким образом определяется среднее удлинение на стандартной длине l0 = 10d. В некоторых случаях за l0 принимается длина, равная 5d.
![]() |
????????? ??? ??????? ????? ?????????:
Возникающие деформации распределены по длине образца неравномерно. Если произвести обмер отрезков, расположенных междусоседними рисками, можно построить эпюру остаточных удлинений, показанную на рис. 7. Наибольшее удлинение возникает в месте разрыва. Оно называется обычно истинным удлинением при разрыве.
Диаграмма растяжения, построенная с учетом уменьшения площадиF и местного увеличения деформации, называется истинной диаграммой растяжения (криваяOC'D' на рис. 8).
Рис. 8 D’
Пластичность и хрупкость. Твердость
Способность материала получать большие остаточные деформации, не разрушаясь, носит название пластичности. Свойство пластичности имеет решающее значение для таких технологических операций, как штамповка, вытяжка, волочение, гибка и др. Мерой пластичности является удлинение d при разрыве. Чем больше d, тем более пластичным считается материал. Противоположным свойству пластичности является свойство хрупкости, т. е. способность материала разрушаться без образования заметных остаточных деформаций. Материалы, обладающие этим свойством, называются хрупкими. Для таких материалов величина удлинения при разрыве не превышает 2—5%, а в ряде случаев измеряется долями процента. К хрупким материалам относятся чугун, высокоуглеродистая инструментальная сталь, стекло, кирпич, камни и др. Диаграмма растяжения хрупких материалов не имеет площадки текучести и зоны упрочнения (рис. 9).
Рис. 9
По-разному ведут себя пластичные и хрупкие материалы и при испытании на сжатие. Как уже упоминалось, испытание на сжатие производится на коротких цилиндрических образцах. Для малоуглеродистой стали диаграмма сжатия образца имеет вид кривой, показанной на рис. 10. Здесь, как и для растяжения, обнаруживается площадка текучести с последующим переходом к зоне упрочнения. В дальнейшем, однако, нагрузка не падает, как при растяжении, а резко возрастает. Происходит это в результате того, что площадь поперечного сечения сжатого образца увеличивается; сам образец вследствие трения на торцахпринимает бочкообразную форму (рис. 11). Довести образец пластического материала до разрушения практически не удается. Испытуемый цилиндр сжимается в тонкий диск (см. рис. 11), и дальнейшее испытание ограничивается возможностями машины. Поэтому предел прочности при сжатии для такого рода материалов найден быть не может .
Рис. 10 Рис. 11
Иначе ведут себя при испытании на сжатие хрупкие материалы. Диаграмма сжатия этих материалов сохраняет качественные особенности диаграммы растяжения (см. рис. 9). Предел прочности хрупкого материала при сжатии определяется так же, как и при растяжении. Разрушение образца происходит с образованием трещин по наклонным или продольным плоскостям (рис. 12).
Рис. 12
![]() |
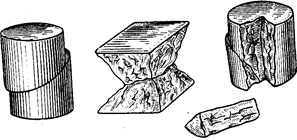
для чугунаk колеблется в пределах 0,2 ¸ 0,4. Для керамических материалов k = 0,1 ¸ 0,2.
Для пластичных материалов сопоставление прочностных характеристик на растяжение и сжатие ведется по пределу текучести (sтр и sтс ).Принято считать, что sтр »sтс .
Существуют материалы, способные воспринимать при растяжении большие нагрузки, чем при сжатии. Это обычно материалы, имеющие волокнистую структуру, — дерево и некоторые типы пластмасс. Этим свойством обладают и некоторые металлы, например магний. Деление материалов на пластичные и хрупкие является условным не только потому, что между теми и другими не существует резкого перехода в показателе d. В зависимости от условий испытания многие хрупкие материалы способны вести себя как пластичные, а пластичные — как хрупкие.
Очень большое влияние на проявление свойств пластичности и хрупкости оказывает время нагружения и температурное воздействие. При быстром нагружении более резко проявляется свойство хрупкости, а при длительном воздействии нагрузок — свойство пластичности. Например, хрупкое стекло способно при длительном воздействии нагрузки при нормальной температуре получать остаточные деформации. Пластичные же материалы, такие, как малоуглеродистая сталь, под воздействием резкой ударной нагрузки проявляют хрупкие свойства.
Одной из основных технологических операций, позволяющих изменять в нужном направлении свойства материала, является термообработка.Известно, например, что закалка резко повышает прочностные характеристики стали и одновременно снижает ее пластические свойства. Для большинства широко применяемых в машиностроении материалов хорошо известны те режимы термообработки, которые обеспечивают получение необходимых механических характеристик материала.
Испытание образцов на растяжение и сжатие дает объективную оценку свойств материала. В производстве, однако, для оперативного контроля над качеством изготовляемых деталей этот метод испытания представляет в ряде случаев значительные неудобства. Например, при помощи испытания на растяжение и сжатие трудно контролировать правильность термообработки готовых изделий. Поэтому на практике большей частью прибегают к сравнительной оценке свойств материала при помощи пробы на твердость.
Под твердостью понимается способность материала противодействовать механическому проникновению в него посторонних тел. Понятно, что такое определение твердости повторяет, по существу, определение свойств прочности. В материале при вдавливании в него острого предмета возникают местные пластические деформации, сопровождающиеся при дальнейшем увеличении сил местным разрушением. Поэтому показатель твердости связан с показателями прочности и пластичности и зависит от конкретных условий ведения, испытания.
Наиболее широкое распространение получили пробы по Бринелю и по Роквеллу. В первом случае в поверхность исследуемой детали вдавливается стальной шарик диаметром 10 мм, во втором — алмазный острый наконечник. По обмеру полученного отпечатка судят о твердости материала. Испытательная лаборатория обычно располагает составленной путем экспериментов переводной таблицей, при помощи которой можно приближенно по показателю твердости определить предел прочности материала. Таким образом, в результате пробы на твердость удается определить прочностные показатели материала, не разрушая детали.