Курсовая работа: Расчет и проектирование циклона для очистки от зерновой пыли
2.1 Созревание и послеуборочное дозревание зерна
Сущность процесса созревания зерна состоит в том, что растворимые в воде низкомолекулярные вещества, образовавшиеся в зеленых листьях и стеблях, перемещаются в зерно. Сахара, находившиеся в зерне на его ранних стадиях созревания, превращаются в крахмал и гемицеллюлозу, из свободных аминокислот синтезируются белки, идет формирование клейковины. Свежее убранное зерно имеет пониженные семенные и технологические качества. Полная физиологическая зрелость зерна, при которой оно отличается наивысшей всхожестью и энергией прорастания, наступает через некоторое время в процессе его хранения. Этот период называется периодом послеуборочного дозревания. Зерно наиболее быстро дозревает при низкой влажности, температуре 15-30С° и выше и свободном притоке воздуха к семенам. Кислород не только ускоряет этот процесс, но и ведет к удалению диоксида азота образующегося при дыхании зерна и замедляющего эту стадию.
2.2 Сушка зерна в зерносушилке
При неблагоприятных условиях хранения процесс послеуборочного дозревания пшеницы требует 1-1,5 месяцев, а при искусственной сушке его можно сократить до 2-3 недель. Для ускорения процесса дозревания применяют зерносушильные аппараты.
Зерносушильный агрегат ДСП-32-ОТ открытого типа предназначен для сушки сырого зерна кукурузы, пшеницы, ржи, ячменя, овса, семян подсолнечника и других зерновых культур.
Зерносушильный агрегат такого типа (рис. 2) состоит из двух параллельно работающих шахт 3 высотой 11,57 м. Каждая из них состоит из семи секций по высоте делится на три зоны: первая зона сушки высотой 4,95 м расположена на верхней части шахты; вторая зона сушки высотой 2,85 м находится в средней части шахты; третья зона является охладительной. Высота одной секции составляет 1,65 м, причем в каждой секции расположено 8 рядов коробов по 16 в каждом ряду. Шахта по высоте имеет пеногасителями сплавного устройства и частично увлекается водой в канал. Примеси из моечной ванны через воронку 8 и патрубок 9 отводятся в сборник. В отжимной колонке под действием центробежной силы и вихревых потоков воздуха влажное зерно прижимается к ситовой обечайке и поднимается лопатками барабана 19 к выпускным патрубкам. Из отжимной колонки зерно поступает на дальнейшую обработку.
Технологическая схема подготовки зерна к помолу (см. чертеж) может быть сокращенной или развернутой в зависимости от типа зерновой культуры, ее качества, типа помола и т. д. Для сортового помола пшеницы применяют развернутую схему, которая включает в себя следующие стадии: сушка зерна в зерносушилке, отлежка зерна на складе, взвешивание, магнитный контроль, сепарирование, выделение минеральных примесей на камнеотделительной машине, магнитный контроль, обработку поверхности на обоечных машинах, гидротермическая обработка зерна (аспирационная колонка А1-БКА), увлажнение и мойка зерна, короткая отлежка.
2.3 Помол зерна
Помол зерна состоит из двух операций: собственно помола зерна и просеивания продуктов помола. Помолы могут быть разовыми и повторительными.
Разовый помол - наиболее простой, при этом зерно на молотковых дробилках за один прием полностью измельчают в муку вместе с оболочками. Полученная мука отличается низким качеством, имеет темный цвет, неоднородна по размеру частиц. Для улучшения качества муки разового помола из нее путем просеивания отбирают некоторое количество крупных оболочек (отрубей). Разовые помолы имеют ограниченное применение.
Повторительные помолы более совершенны, зерно измельчают в муку путем многократного прохождения через измельчающие машины, при этом после каждого измельчения продукт сортируют в просеивающих машинах.
Основным видом измельчающего оборудования для этих помолов являются вальцовые станки. Два цилиндрических чугунных вальца 2 одинакового диаметра расположены под углом и вращаются навстречу друг другу с разными скоростями. Поверхность вальцов рифленая, зазор между ними устанавливается в зависимости от намечаемой крупноты помола. Исходное зерно через приемную трубу 5 питающим механизмом 3 подается на вальцы 2. Зерно задерживается нижним вальцом, имеющим меньшую скорость вращения, скалывается и растирается рифлями верхнего быстровращающегося вальца.
Чувствительный элемент сигнализатора уровня 4, шторки-датчики 6 и заслонка 7 служит для регулирования подачи зерна. Поверхность вальцов очищается с помощью щеток 1 и ножей 8. Измельченное зерно II удаляется через выпускные конусы 9. Для сортирования продуктов измельчения зерна по размеру частиц после каждого вальцового станка устанавливается рассев с набором сит разных размеров, расположенных друг под другом.
3. Расчет циклона
???????? ?????? (???? ????????):1) ?????????? ?????????? ???? ??? ??????? ???????? Qр = 3800 ?3 /? = =1,05 ?3 /?;2) ????????? ???? ??? ??????? ???????? ρг = 1,3 ??/?3 ;3) ???????????? ???????? ???? ??? ??????? ??????????? μt = 22,2*10-6 ????;4) ?????????? ?????? ????, ?????????? ????? ??????????? dm = 5 ??? ? lg σч = 0,283;5) ???????????? ???? ?вх = 10 ?/?3 ;6) ????????? ?????? ρч = 1100 ??/?3 ;7) ????????? ????????????? ??????? ???? η = 80 %.?????? ???????? ???????????? ??????? ???????????????? ??????????? ? ????????? ???????:1. ????????? ????? ??????? (??-15?), ?? ??????? 2.8 [1] ?????????? ??????????? ???????? ???? ? ???????? ωопт = 3,5 ?/?.2. ?????????? ??????????? ??????? ??????? ???????, ?2 :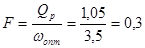
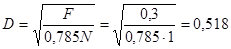



6. Определяем потери давления в циклоне, Па:
7. Приняв по таблице 2.8 два параметра, характеризующих эффективность выбранного типа циклона, определяем значение параметра d50 при рабочих условиях (диаметр циклона, скорость потока, плотность пыли, динамическая вязкость газа) по уравнению:
8. Определяем параметр Х по формуле:
9. Определяем по таблице 1.11 значение Ф(Х ), представляющее собой полный коэффициент очистки газа, выраженный в долях:
Ф (0,66) = 0,497
10. Фактическая степень очистки, %:
Для проектирования и построения циклона необходимы геометрические размеры. Для этого используем табл. 1.13 [2] “Соотношение размеров (в долях внутреннего диаметра)”:
Внутренний диаметр выхлопной трубы d = 0,3 м;
Внутренний диаметр пылевыпускного отверстия d1 = 0,2 м;